An experimental bloomery smelt by Owen Bush
A Report by Tim Smith
On 20th August a small group of WIRG members and two members of the Wadhurst History Society (who had attended the WIRG Summer meeting at Ticehurst) congregated at East Wickham Farm in Welling, Kent (almost within sight of the Thames Dartford crossing) to witness a smelt by two professional blacksmiths, Owen Bush and Mick Maxen.
Owen had attended the WIRG visit to the excavations at Upper Wilting Farm (near Hastings) in July and we told him of our smelting experiments at Pippingford, whereupon Owen revealed he too was a smelter and invited WIRG along to his next smelt. We happily agreed but with the proviso that Owen should smelt the same local Wealden ore that we are currently using rather than the much richer imported ores he normally uses.
Owen rose to the challenge with such enthusiasm that a few weeks later he was guided by one of our experimental smelter, Victor to our ore source in the Beacon Wood stream in Kent where, with the help of Victor and Owen’s students, they collected 800kg of ore.
After roasting, typically this siderite ore contains around 38% iron, but this, and the other constituents present, vary from piece to piece (Table 1).
Table 1 Wet chemical analysis of ore, tap slag and bloom slag skin
Major Components % | BWS Ore | Tap Slag | Bloom Slag skin* |
Volatiles | 31.3 | 0.38 | 0 |
SiO2 | 6.02 | 21.23 | 6.94 |
Al2O3 | 2.37 | 14.57 | 19.19 |
Fe2O3 | 53.79 | 15.72 | 17.86 |
FeO | - | 37.29 | 40.61 |
CaO | 1.46 | 8.73 | 8.80 |
MgO | 0.01 | 0 | 0 |
MnO | - | 0.10 | 0.09 |
Not Determined | 5.22 | 1.98 | 6.51 |
Totals % = | 100.00 | 100.00 | 100.00 |
Total Fe Content % = | 37.64 | 38.00 | 44.08 |
Ore Bloom Potential (Fe:Si) | 13:1 | - | - |
Owen modifies his furnace design and smelting technique depending on the ore he is using. For the Kent ore, he used a ‘thin’ walled (~40mm thick) cylindrical shaft furnace about 1.5m high and 300mm internal diameter. The furnace walls were made of a mixture of China clay, old furnace wall grog and 'other' clay. The construction follows the American technique of Lee Sauder and Skipp Williams which use a very high blowing rate. (Owen has spent time smelting with Lee and Skipp).
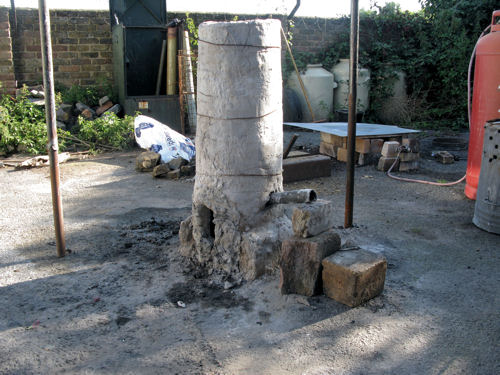
Thin walled clay shaft furnace
The aim of running the furnace with hot walls is to prevent reaction between the slag formed and furnace walls to avoid sticking to the wall. The base of the furnace was first lined with wood ash to prevent slag sticking to the base to aid subsequent clearing of the furnace, and a bed of fine charcoal was built up on this to within about 50mm of the tuyere . The tuyere was a thick walled (~5mm) copper tube of internal diameter about 20mm and inclined downwards at 17 deg. This was inserted to about 50mm beyond the inner wall. The tapping arch was completely sealed with clay.
There is no claim by Owen that this technique represents an authentic method of early smelting, rather he is interested in producing a good bloom of forgeable iron.
The furnace was preheated with a propane gas torch for about 40 minutes. No temperatures were recorded as Owen prefers to rely on his eye to judge temperature.
When the inside top of the furnace was glowing red the torch was removed, the first charge of charcoal – made from imported hard wood - added, and the electric blower turned on. The first charge of ore was prepared weighing out 2kg charcoal and separately 2kg roasted ore crushed to about 10mm size and smaller. The charcoal was charged and the ore sprinkled in over the following 15 minutes or so, a little at a time. Meanwhile, the next charge was prepared and the process repeated – charging all 2kg of charcoal first followed by the ore bit by bit over the next 15 minutes. From the rate of consumption of the charcoal, Jonathan has calculated the blowing rate at about 14.5 litres/sec.
After 4-5 charges, viewing down the tuyere showed droplets of slag falling past its end.
After about 17kg of ore had been added a ‘burbling’ sound could be heard from the furnace indicating some slag build up. At this point Owen tapped the slag by pushing a ~12mm diameter square steel rod through the clay of the tapping arch near the base. On withdrawing this, slag flowed ‘like milk’ onto the ground in front of the furnace solidifying into a very porous friable layer.
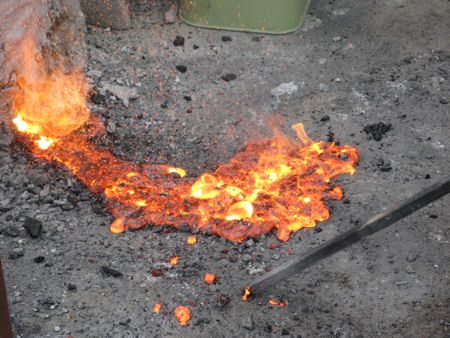
Tap slag flowing from 10mm diam hole made in closed slagging arch
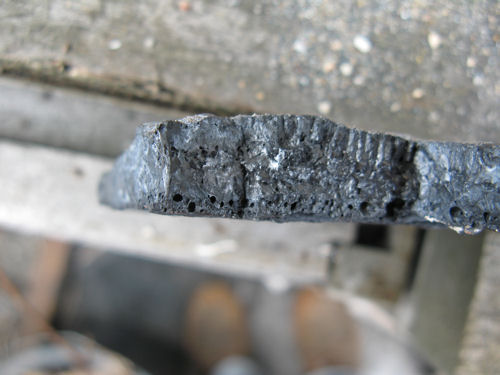
Cross section of the cooled tap slag
As the smelt progressed, further holes were made in the tapping arch clay to release more slag. A sample was taken of the slag from the second tap and later analysed (Table 1 above). As smelting progressed, the tapping arch was opened further to enable Owen to prod the bottom of the bloom to release more slag.
After 50kg of ore had been added, charging ceased and the charge allowed to burn down to a little above tuyere level. Blowing was then stopped and the slagging arch fully opened through which the bloom was extracted using tongs. While Owen held and turned this on the ground Mick hammered it to break off adhering slag leaving a bloom weighing around 12kg. Samples of this were taken for later analysis (Table 1). Owen then transferred the red hot bloom to a power hammer to start the consolidation process.
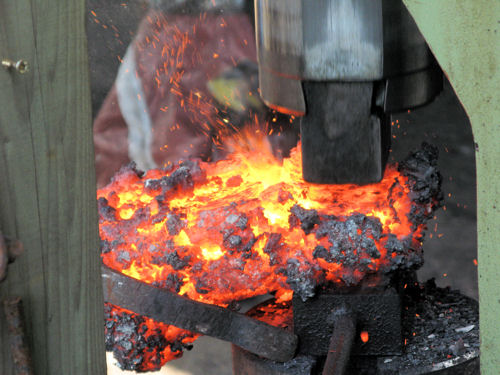
Consolidation of the bloom
The anvil of the power hammer (at about 150 x 75mm) was much smaller than the bloom which caused it to splay out and fragment broke off. Owen reheated the largest piece to a bright orange heat in a small enclosure of fire bricks heated by a propane torch and then continued with consolidation. Repeating this process several times, he drew out a bar of iron about 50mm wide, 10mm thick and 300mm long, sprinkling a little borax flux on the hot metal to aid forge welding of cracks.
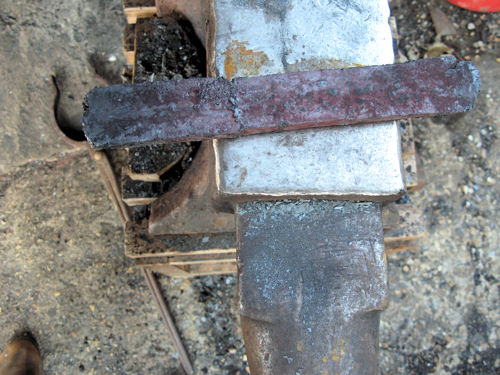
Final drawn bar from a piece of the bloom
When cool, sparking this on a grinding wheel indicated a ‘low carbon’ iron. Subsequent analysis indicated a carbon content of about 0.16% (Table 2). A fracture test on the iron showed it to be ductile, again confirming the low carbon content and a subsequent hardness test gave a result of 200 on the Vickers pyramid indentation scale (VPN), which again indicates a relatively soft iron.
Owen has found that the fragments of broken bloom contained forgeable iron. These, and the consolidated piece together weighed around 12kg indicating a 24% yield from the roasted ore, but taking into account the iron content of this as 38%, – the yield from the available iron is 63% ie 12/(50x0.38).
Subsequent forging of the iron by Owen indicates the iron to be ‘hot short’ ie tends to break up on forging at orange heat. This is normally an indication of a high sulphur content – an element which unfortunately we are unable to determine with our analytical facilities.
The results prove that workable iron and a tapable slag can be achieved using Wealden ore, although we have still a long way to go to match the standards of the ancients.
Micrography showed much of the iron as metallic iron
Table 2. Wet chemical analysis of bloom
Carbon % | Si % | Mn % | Fe % | Total % |
0.16 | 0.92 | 0.43 | 98.55 | 100.06 |
Micrographs of the tap slag show it to be far richer in wustite (FeO) than what is generally found in the field (Fig 1).
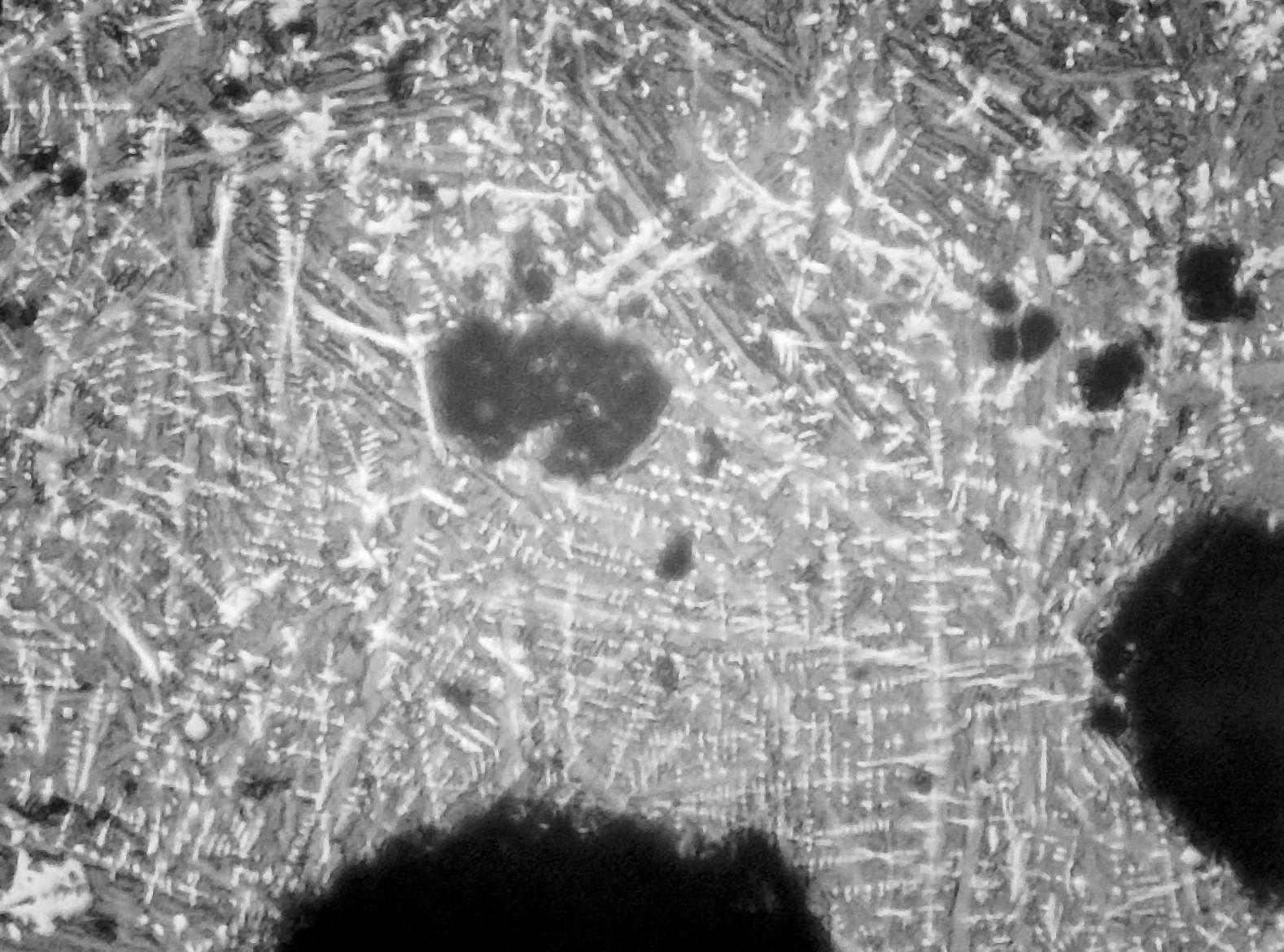
Fig 1. Tap slag x 100 showing high proportion of wustite dendrites (white)
A micrograph of the consolidated bloom shows the presence of free carbides indicating a non-equilibrium structure since all the carbon present would normally occur as a lamellae structure of carbide and ferrite (pure iron) called pearlite (Fig 2).
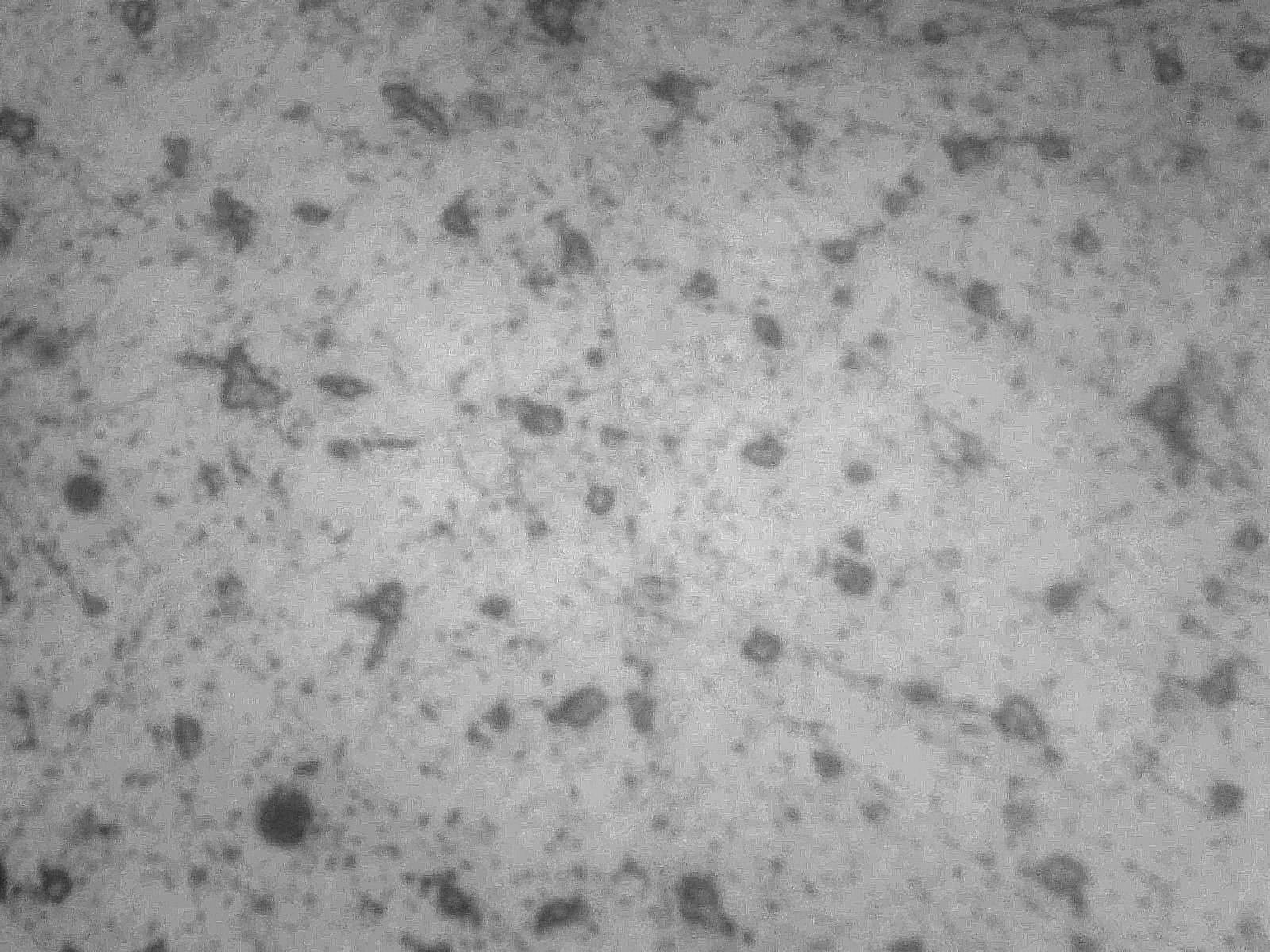
Fig 2 Worked bloom showing isolated areas of iron carbide (Fe3C) in matrix of ferrite x400
There are also stringers of slag present drawn out by the forging process (Fig 3)
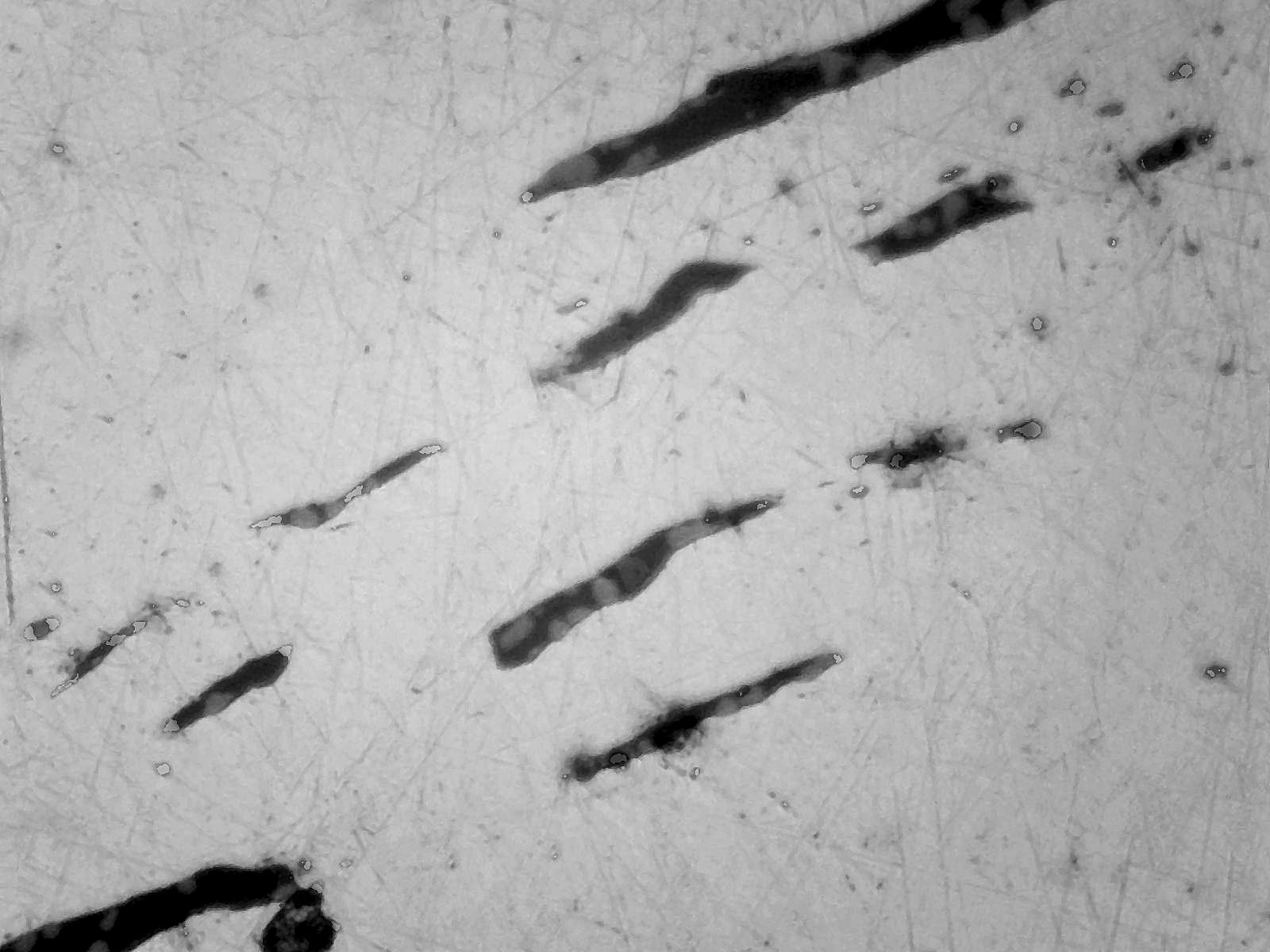
Fig 3 Stringers of slag in worked bloom x100
For further information on analysis, please email Alan Davies:
.
For further information on smelting, please email Tim Smith:
.
© Wealden Iron Research Group 2014
|